-
• Advanced technology to process LDPE material and Ocean Bound Plastic.
-
• Reduced landfill-bound plastic, carbon footprint, and reliance on new plastics.
-
• Certifications for ISO 9001:2015, 14001:2015, 45001:2018, Global Recycled Standard (GRS), and Ocean Bound Plastic Standard.
ReSL’s plastic recycling plant in Visakhapatnam manages Low-Density Polyethylene (LDPE) liner waste from pharmaceutical industries, countering environmental issues linked with plastic disposal. Embracing a circular economy approach, ReSL collects discarded plastic film from pharmaceutical firms, modifies it into uniform raw material through washing and pelletization, and uses it for producing biomedical waste collection bags.
This initiative notably diverts landfill-bound plastic film, lessening environmental impact. Furthermore, the recycling unit’s circular economy model helps reduce reliance on new plastics, conserving resources and reducing the carbon footprint. This case highlights effective waste management and sustainability efforts at our Visakhapatnam recycling facility.
The facility maintains the highest standards of integrated management systems and has certifications for ISO 9001:2015, 14001:2015, and 45001:2018 standards. Additionally, it holds certifications for the Global Recycled Standard (GRS) and the Ocean Bound Plastic Standard.
During FY 2022-23, the plant processed 1,225 MT of LDPE material, produced 348.9 MT of biomedical waste collection bags and collected & processed 206 MT of Ocean Bound Plastic (OBP) material.
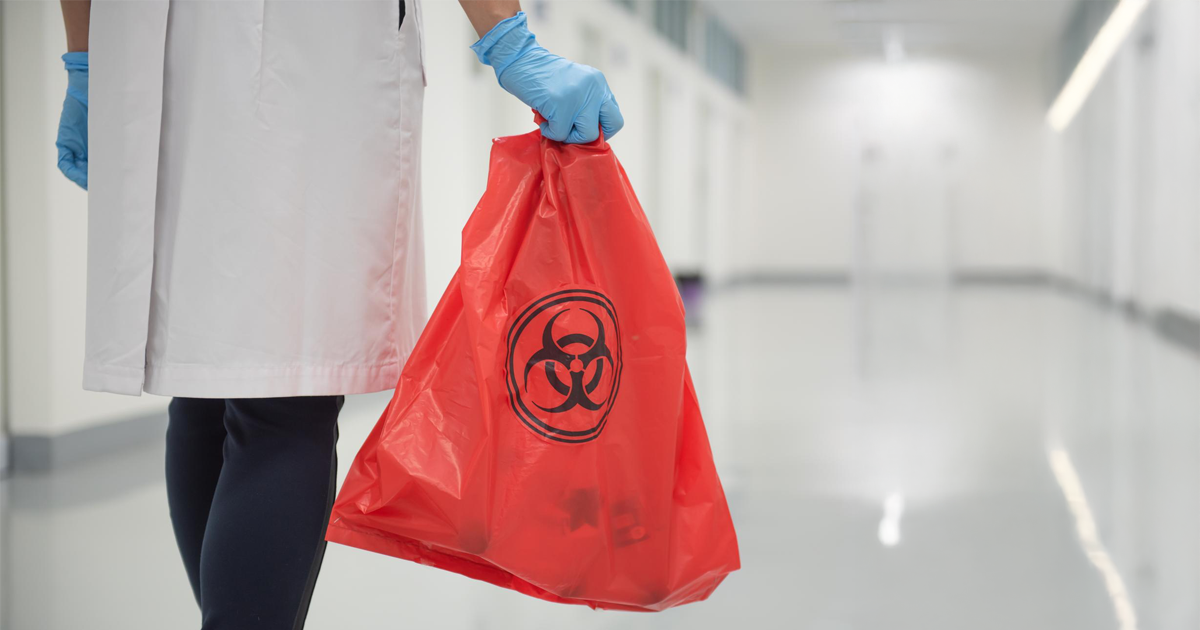
Let's Get
- In Touch